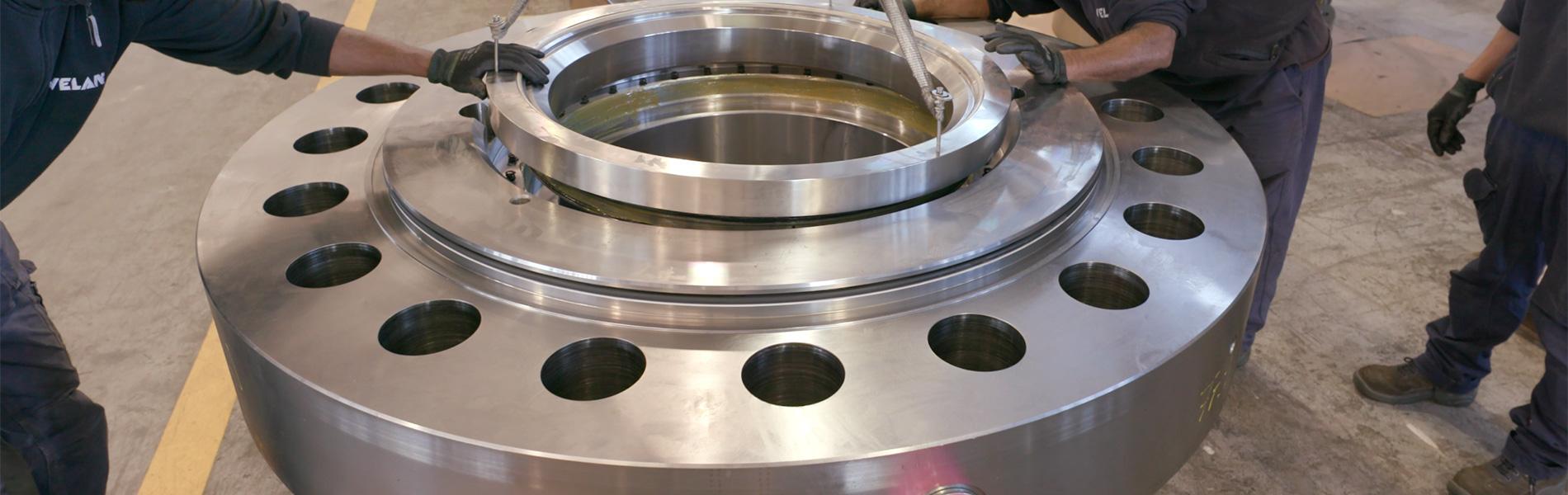
Modular double block and bleed ball valve
API 6D Modular double block and bleed
8 inch. ASME 2500, hub connections, operated by gears
For double isolation in FPSO topside facilities
API 6D Modular double block and bleed
8 inch. ASME 2500, hub connections, operated by gears
For double isolation in FPSO topside facilities
Testing- API 6D Modular double block and bleed
16x14 inch. ASME 2500, Compact flange connections, operated by two Gears
For double isolation in FPSO topside facilities
API 6D Modular double block and bleed
6 inch. ASME 900, RTJ connections,operated by two electric actuators
For double isolation in FPSO topside facilities
API 6D Modular double block and bleed
10 inch. ASME 900, RTJ connections,operated by two gears
For double isolation in FPSO topside facilities
API 6D Modular double block and bleed
12 inch. ASME 1500, RTJ connections,operated by two gears
For double isolation in FPSO topside facilities
API 6D Modular double block and bleed
8 inch. ASME 1500, RTJ connections,operated by two gears
For double isolation in FPSO topside facilities
API 6D Modular double block and bleed
6 inch. ASME 900, RTJ connections,operated by two electric actuators
For double isolation in FPSO topside facilities
BTD-BTC-SSD
based on API 6D or API 6A or API 6DSS and customer requirements
NPS 2-48 (DN 50-1200)
NPS 1.13/16 –16.3/4 (DN 46-425)
RF, RTJ as per B16.5 &B16.47
BW, Butt Welded as per B16.25
Hub connection
6B, 6BX as per API6A
Forged three-piece housing two balls
Soft or metal seated with hard facing on ball and seats
Four Self relieving seats
Four Double piston seats
Combination seats
Double block and bleed design (DBB)
Secondary seals in pure Graphite
Anti-static device
Anti-blowout stem
O-ring / Lip seal configuration
Emergency sealant injection on seats and stem available
Low fugitive emission stem packing available
CRA overlay on all dynamic sealing areas or on all wetted parts available
Extended bonnet for low & high temperature available
Low pressure loss through the valve
BTC series: extremely compact valve design as per high pressure compact ball valves
Manual: wrench or gear with padlocking
Actuated: Pneumatic/ Hydraulic/Electric
Compliance with API 6D & ISO 5208 & API 598 inspection and testing
Compliance with API 6A inspection and testing
Compliance with API 6DSS Inspection and testing
Fire safe and fire tested as per API 6FA/607
SIL 3 Certification as per IEC61508
Fugitive Emission as per ISO15848
PED 2014/68/UE
Available as per API 6A standard:
Product specification levels PSL 1, 2, 3, 3G, and 4
Performance requirement levels PR1, PR2
Design validation as per PR2F
Modular double block and bleed valves combine two in-line isolation valves into a single body with an additional bleed valve used to drain or vent trapped fluid between the two obturators to ensure highest level of safety in double isolation and bleed service. Using a double block and bleed valve versus two separate valves saves weight and space on the piping layout and ensures a significant reduction of potential leakage to the atmosphere, minimizing any hazardous risk when transferring liquids or gas. Several unique features are available to offer advanced technical solutions suitable to deal with aggressive and severe offshore environments. Material selection is fully customizable to meet customers project specifications.